CNC가공은 범용성이 매우 높은 공정이지만 여러 공정과 결합할 수도 있습니다.
이번 포스팅에서는 금속가공분야에서 CNC가공과 병행되는 여러 공정에 대해 알아보겠습니다.
압출 + CNC 가공
압출은 알루미늄, 아연, 구리 합금 등 각종 형상의 단면재, 각종 파이프나 선재 등을 제작할 때 소성이 큰 재료를 강력한 압력으로 한 다이에 통과시켜 가공하는 방식입니다. 압출을 통해 연속 프로파일을 가진 길쭉한 성분이 생성되는데, 품질 표면 마감 및 복잡한 단면이 있는 기능적 구성 요소를 생산하는 효과적인 방법입니다.
원래 압출은 생산물의 형상이나 단면이 제한적인 한계가 있습니다.
하지만 CNC가공을 통해 복잡한 단면과 불규칙한 형상을 가진 부품의 생산이 가능해집니다.
일례로 알루미늄 6061 6063과 같은 소재들은 가단성과 연성을 띠기 때문에 압출에 자주 사용되며 생산물은 대개 환봉 형태로 만들어져 CNC가공의 단골 소재로 쓰이고 있습니다.
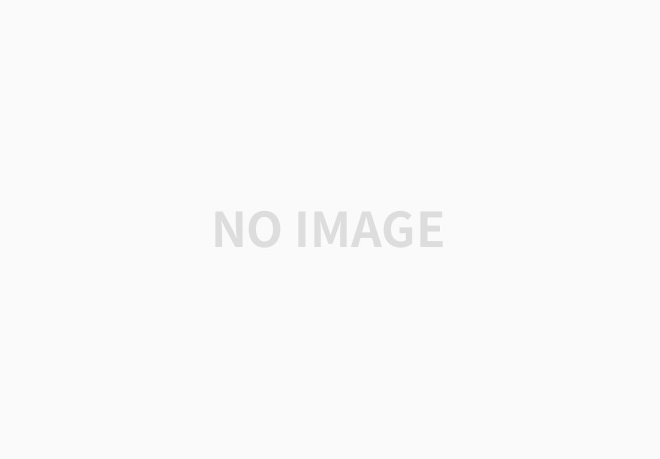
다이캐스팅(압력 주조) + CNC 가공
다이캐스팅은 금형에 금속을 녹여서 높은 압력으로 밀어 넣어 형상을 만드는 공법입니다. 이때 금속재질의 다이(금형)의 가공비용이 높게 들지만 대량생산에서 이점이 있어서 금속소재 제품의 대량생산에 일반적으로 사용됩니다.
철강, 마그네슘 및 아연과 함께 알루미늄은 다이캐스팅에서 가장 인기있는 금속 중 하나이며 다이캐스트 알루미늄 부품은 일반적으로 표면 마감 및 치수 일관성이 뛰어납니다.
이러한 장점은 복잡하고 정밀한CNC 가공과 결합될 때 더욱 극대화될 수 있습니다. 공작기계를 사용하여 컷을 추가함으로써 두 공정을 각각 단독으로 사용할 때보다 뛰어난 마감과 더 복잡한 형상 혹은 생산성 있는 부품을 만들 수 있습니다. 예를 들어 42mm홀이 있는 부품을 만들 때 40mm의 홀이 포함된 주조물을 42mm로 보링 가공하는 것이 더 효율적일 수 있습니다. 물론 기계 별 공작물 셋업 시간에 따른 변수를 고려해야 합니다.
사실 주조만으로는 마감이나 정밀도가 고객사 요구사항을 충족하지 못해, 후가공을 필요로 하는 경우가 많은 점은 널리 알려진 사실로 이를 보완하기 위한 정밀주조를 이용하거나 다이캐스팅을 정밀화 하기위한 기술은 꾸준히 개발되고 있습니다.
단조+ CNC 가공
단조는 소성 가공의 일종으로 해머 등으로 금속 가공물을 두드려 원하는 형태로 성형하는 것을 말합니다. 주조 등 기타 가공 방식보다 충격에 강한 소재를 만들 수 있습니다.
특히나 열간 단조 공정을 거치는 경우 치수 정밀도가 떨어지고 CNC 가공등을 통한 절삭이 필연적이며 냉간 단조의 경우에도 CNC가공이 필요한 경우가 발생할 수 있습니다.
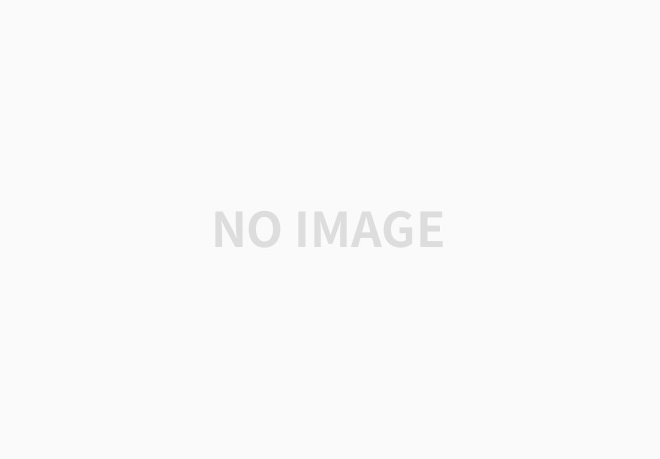
3D프린팅+CNC가공
적층가공의 대표주자인 3D프린팅과 절삭가공에 해당되는 CNC가공은 서로가 상반되는 가공방식인 만큼 상호보완의 여지가 있습니다. 타이트한 공차를 맞추기 위해 프린트물의 일부는 CNC 가공하는 것이 대표적입니다. 재료낭비를 최소화할 수 있다는 장점 또한 존재합니다.
금속가공 분야에서 CNC가공과 다른 공정을 결합한다는 것은 대개 경제성 높게 만들어진 1차 가공물의 마감/정밀도 등을 높이는 효과가 있다고 이해할 수 있습니다. 물론, 개별 공정에 대한 이해와 기계 장비 보유 및 셋업 지식이 필요한 점을 고려할 때 공정 결합이 부담스럽게 느껴지는 것은 사실입니다. 하지만 경우에 따라서 비용을 절감하고 충분한 물성치를 뽑아 내기 위해 이러한 방안들도 존재한다는 사실은 명확히 인지해야 합니다.
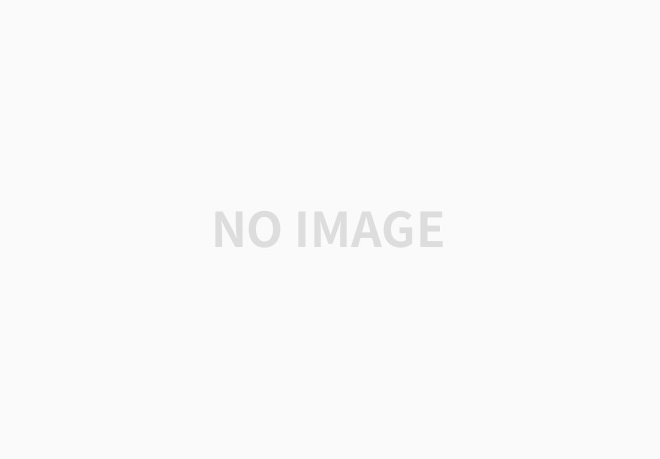
'바로발주 | 제조지식' 카테고리의 다른 글
밀링과 선반 외의 다른 CNC 기계 종류 (0) | 2023.08.07 |
---|---|
플라스틱 가공 재료 - 아크릴(PMMA) (1) | 2023.08.04 |
CNC가공 2축, 3축, 5축의 차이! (0) | 2023.08.04 |
CNC 가공 알아보기 (0) | 2023.08.04 |
CNC 부품의 품질 검사에 대해 알아보기 (0) | 2023.08.04 |